Why should you recoat box coolers?
Why should you recoat box coolers?
Learn how recoating protects box coolers from corrosion and fouling, restores performance and supports sustainable maintenance at sea.
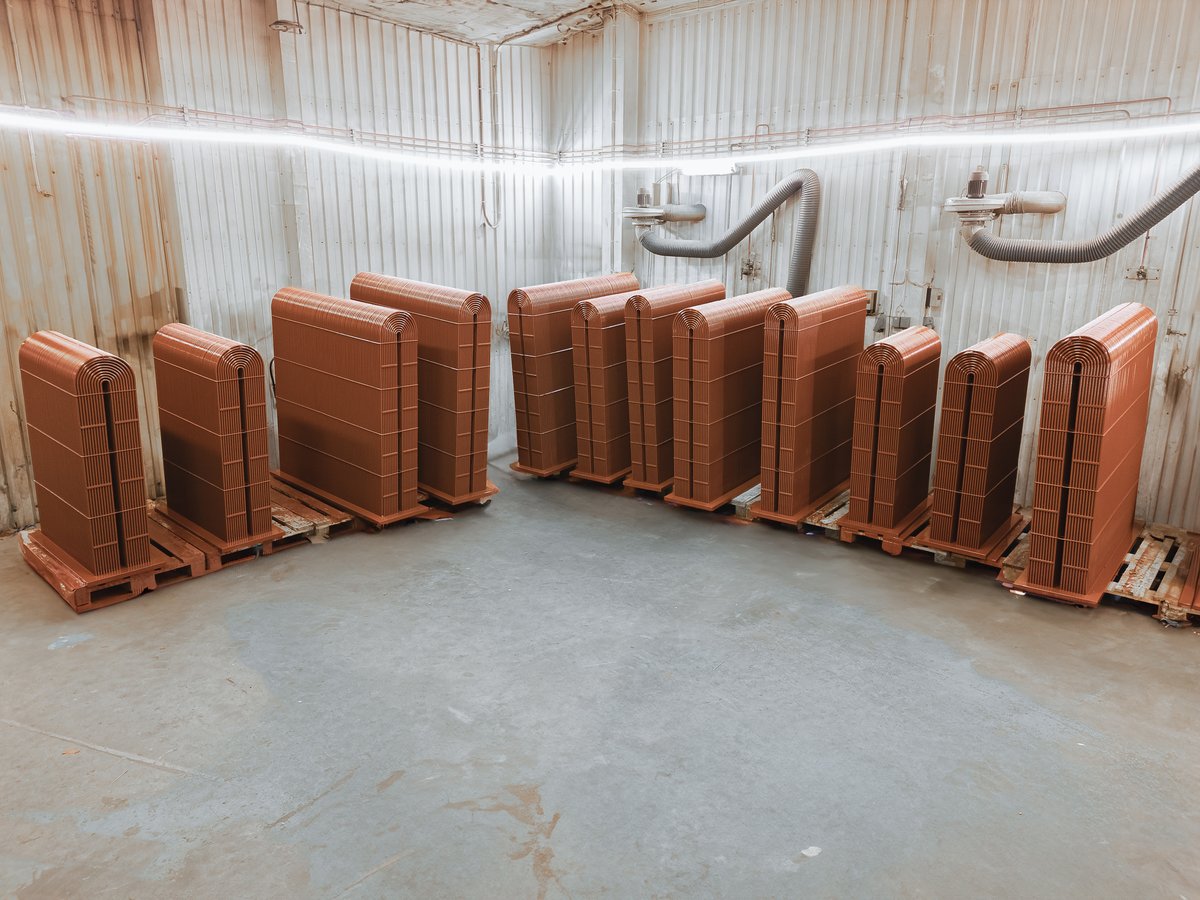
Box coolers are essential components in marine engine cooling systems, providing efficient heat exchange between internal freshwater circuits and seawater. Over time, these units are exposed to corrosive environments and marine growth that reduce cooling capacity, increase maintenance demands, and introduce structural risks—particularly in sea chests where dissimilar metals are present.
Recoating is an established method for mitigating these issues. By applying a protective marine-grade coating to the external surfaces of the cooler, it is possible to prevent galvanic corrosion, reduce fouling, and extend the usable lifespan of the equipment without replacement.
The role of recoating
Galvanic isolation
Many box coolers are manufactured with aluminium-bronze or other high-performance alloys. When installed in steel sea chests, galvanic coupling can occur, accelerating corrosion of adjacent structures. A properly selected and applied coating acts as an electrical barrier, interrupting this reaction.
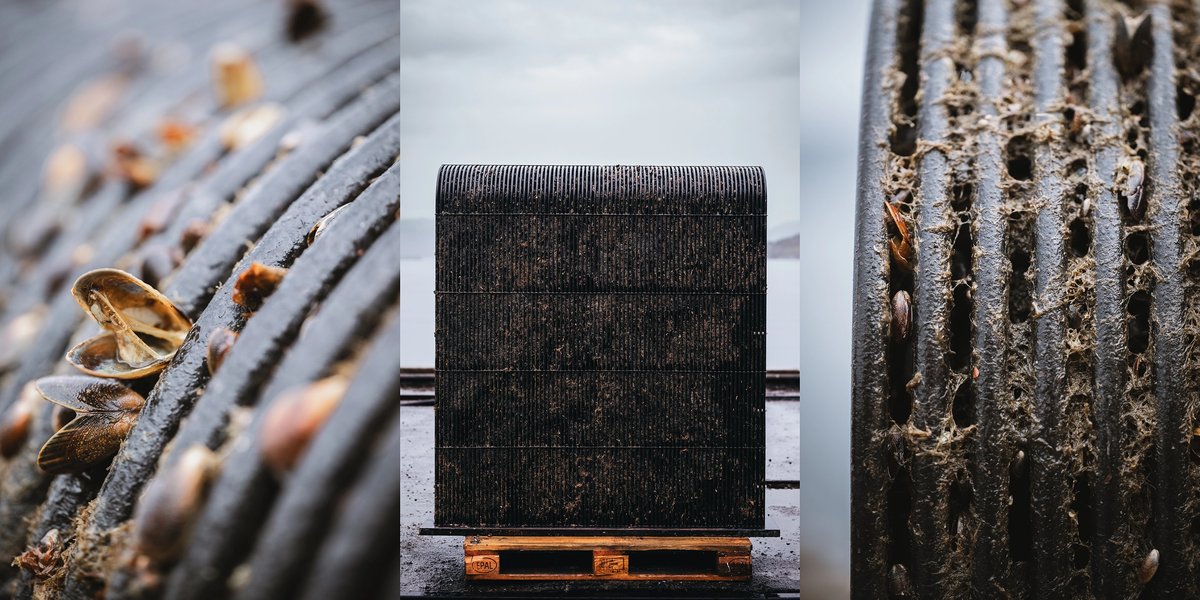
Marine fouling on box coolers
Marine fouling resistance
Biofouling caused by algae, barnacles, and bacterial growth impairs thermal transfer and increases drag on cooling performance. Smooth, hydrophobic coatings help prevent attachment and are easier to clean, reducing system load and cleaning frequency.
Preserving thermal function
Even minor deposits or surface damage can reduce thermal efficiency. Recoating restores surface condition and maintains consistent performance between maintenance intervals.
Our process
NGP provides a full-service recoating solution for marine and offshore clients, ensuring each step is performed according to technical standards and operational requirements:
Inspection and cleaning
Each box cooler is thoroughly inspected and cleaned of all organic and inorganic deposits. Previous coatings and corrosion layers are removed to expose a clean substrate.
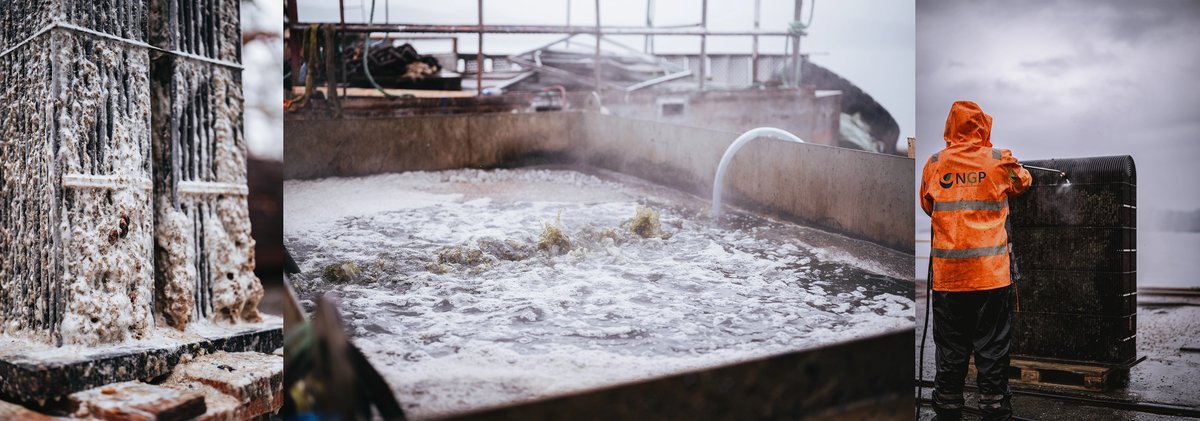
Cleaning of box coolers with Marine Cleaner in dipping tray and rinsing of with HP washer.
Surface preparation
Surfaces are prepared by sandblasting, providing the necessary roughness and cleanliness for proper coating adhesion.
Coating application
A marine-grade protective coating is applied under controlled conditions. All products used are free of biocides and heavy metals, and compliant with applicable IMO and IACS requirements.
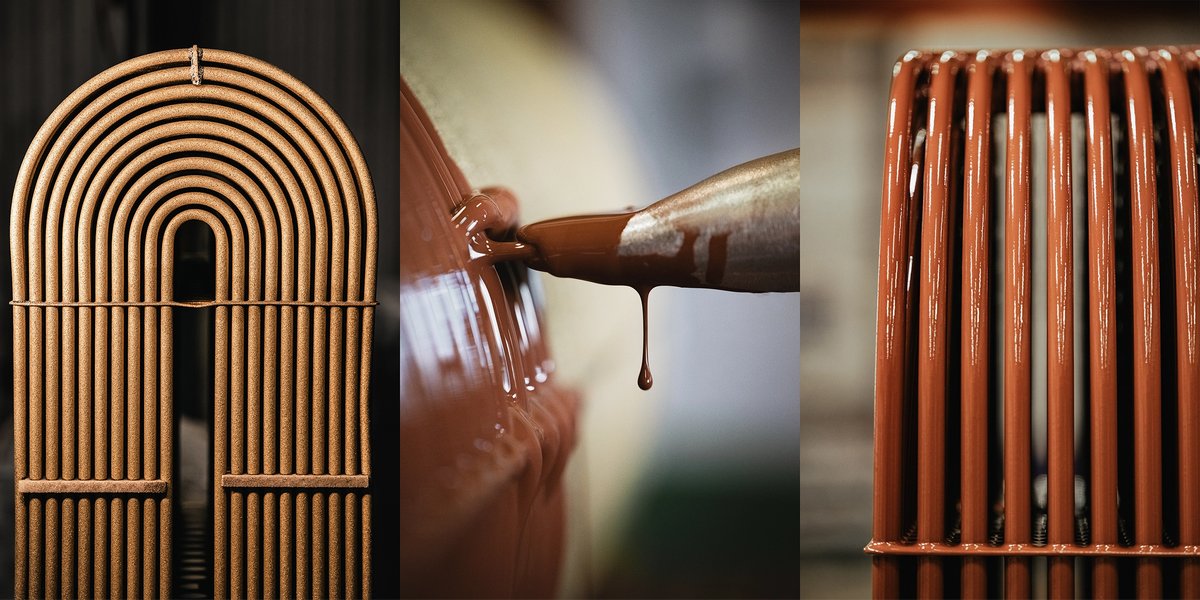
Sandblasted, to recoated box cooler.
Reinstallation and testing
The cooler is reinstalled, sealing surfaces are verified, and pressure testing is performed to confirm system integrity prior to reactivation.
Sustainable protection
All coatings used in our process are environmentally friendly, formulated without toxic biocides or persistent substances. This makes them suitable for modern shipyards and offshore operations that must comply with strict environmental standards.
Conclusion
Recoating is a cost-effective and technically reliable way to preserve the performance and structural integrity of box coolers in marine environments. For vessels and platforms operating in corrosive or high-fouling waters, regular recoating can significantly reduce unplanned downtime, lower maintenance costs, and avoid premature equipment replacement.
As part of the recoating process, NGP performs pressure testing to verify cooler integrity before return to service. We also offer box cooler service kits to support long-term maintenance and operational readiness.
Contact us to learn more about how recoating can be integrated into your fleet’s service strategy.